Discover Premium Ceramic Products | Durability & Elegance United | Advanced Ceramics
PRODUCT PARAMETERS
Description
Overview of zirconia ceramic Nozzles
Zirconia nozzles are specially designed components made of zirconium dioxide (ZrO2) that provide outstanding performance in the most demanding of applications due to their distinctive characteristics as a material. These nozzles are commonly employed in industries which require materials that are that can withstand high temperatures, harsh environments, or mechanical wear.
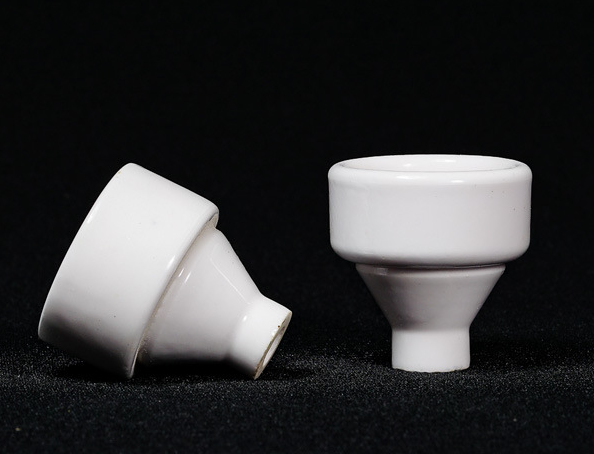
Features of zirconia ceramic Nozzles
1.High-Temperature Resistance
Zirconia can endure temperatures up to 2200 degrees Celsius in oxidizing conditions.
Benefit: It’s ideal for processes which require high temperatures, such as metal casting glass production and chemical processing, that provide high performance and long-term stability.
2. Excellent Chemical Inertness
The feature is highly resistant to bases, acids and molten Ls.
Benefit: Reduces the risk of corrosion and contamination, thus prolonging the life of the nozzle while ensuring the purity of the product.
3. Superior Thermal Shock Resistance
Features: Designed to withstand extreme temperature variations without cracking or breaking.
The benefit is that it’s suitable for use in applications that require thermal cycling, which could reduce the duration of repair or maintenance costs.
4. Low Coefficient of Thermal Expansion
Features Limit expansion and contraction during heat and cooling cycles.
The benefit decreases thermal stress and deformation, which guarantees stability and quality in a variety of temperatures.
5. High Hardness and Fracture Toughness
Specifications: Excellent toughness and hardness, especially when stabilized with additives like yttr IA.
Benefit: Provides excellent durability and wear resistance. Also, make zirconia-based sprayers suitable for harsh and high-pressure environments.
6. Electrical Insulation
Features Great electrical insulation even at room temperature.
Benefit: Suitable for applications that require isolation of electrical power for certain kinds of sensors as well as components in electronic devices.
7. Oxygen Ion Conduction at High Temperatures
Features: Conducts oxygen ions efficiently even at higher temperatures.
Benefit: Beneficial for applications such as Solid oxide fuel cells (SOFCs) and oxygen sensors, improving performance and efficiency.
8. High Purity
Features: Available in ultra-pure forms with low impurities.
Benefit It ensures that the nozzle is not introducing substances into the procedure. This is essential to maintain the integrity and quality of the product.
9. Mechanical Strength
Features: High stretch and compressive strength.
Benefit: Provides strength and stability of the structure, as well as resists mechanical load even in harsh operating conditions.
10. Dimensional Stability
The feature is minimal shrinkage when sintering and great control of dimensional control.
Benefit: Provides the exact fit and function of high-precision applications, which reduces variation within performance.
11. Corrosion Resistance
Special feature: Extreme resistance to different corrosive Ts.
Benefit: Increases the life span of the nozzle, even in highly chemical environments, while reducing the cost of maintenance and replacement.
12. Smooth Surface Finish
The feature allows for very smooth surface finishes by polishing.
Benefits: Improves flow characteristics and lowers the risk of clogging. This is the reason why vital for processes that require precise materials delivery.
13. Versatility in Design
The feature can be produced in different sizes and shapes to satisfy the specific requirements of an application.
Benefit: Provides the flexibility of design, allowing various volumes, configurations and operational needs.
14. Environmental Stability
Feature: Stable under a wide range of environmental conditions.
Benefit: Reliable performance in diverse laboratory and industrial settings, including those with varying humidity and atmospheric compositions.
15. Biocompatibility
Feature: Some grades of zirconia exhibit biocompatibility.
Benefit: Suitable for use in medical devices and applications where interaction with biological tissues is required.
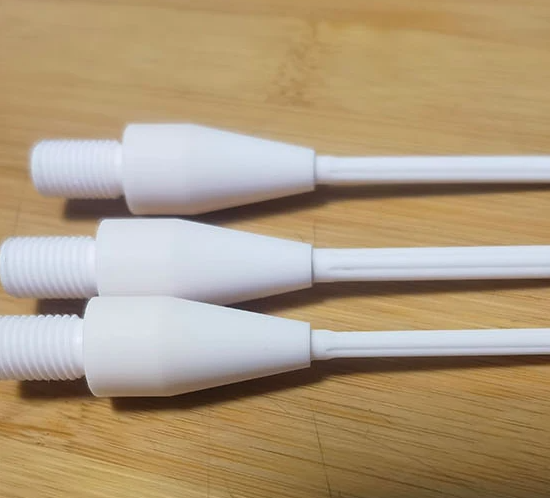
Specifications of zirconia ceramic Nozzles
Specification | Description |
Material Composition | ZrO2 with stabilizers (e.g., Yttria, Magnesia) |
Purity (%) | Typically 95% to 99.95%, depending on grade |
Density (g/cm³) | Approximately 5.60 to 6.10 g/cm³ |
Melting Point (°C) | ~2700°C |
Max Service Temperature (°C) | Up to 2200°C in oxidizing atmospheres |
Thermal Conductivity (W/m·K) | Low, around 1.5 to 3.5 W/m·K at room temperature |
Coefficient of Thermal Expansion (CTE) (10^-6/K) | ~10.5 at room temperature |
Chemical Resistance | Excellent resistance to acids, bases, and molten metals |
Electrical Resistivity (Ω·cm) | High, >10^12 Ω·cm at room temperature |
Surface Finish (Ra µm) | Can range from rough (<50 µm) to highly polished (<0.1 µm) |
Tolerance (mm) | Usually ±0.1 mm for dimensions, depending on size and application requirements |
Nozzle Diameter (mm) | Available in various sizes, from small diameters (a few millimeters) to larger ones |
Nozzle Length (mm) | Varies based on design and application needs |
Wall Thickness (mm) | Typically ranges from 1 to 3 mm |
Shape | Various shapes including straight, tapered, or custom designs |
Fracture Toughness (MPa·m^½) | Around 7 to 12 MPa·m^½ |
Flexural Strength (MPa) | Can range from 800 to 1200 MPa at room temperature |
Porosity (%) | Very low, typically less than 1% |
Oxygen Ion Conductivity (S/cm) | Significant at high temperatures (>800°C) |
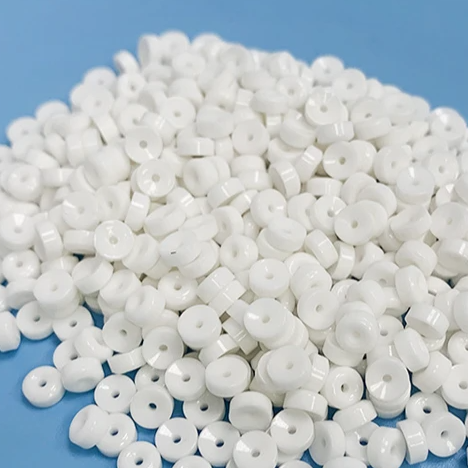
Zirconia ceramic nozzles
Manufacturing Methods of Zirconia ceramic nozzles
1.Powder Preparation
Material Selection: High-purity zirconium dioxide (ZrO2) powder is selected as the base material. Depending on the application, stabilizers like yttria (Y2O3), magnesia (MgO), calcium (CaO), or ceria (CeO2) may be added.
Mixing: The powders are thoroughly mixed using either wet or dry mixing processes to ensure homogeneity. Wet mixing often involves organic binders or dispersants to improve flowability and sintering behaviour.
2. Shaping
Several techniques can be employed to shape the zirconia powder into crucible forms:
Pressing:
Dry Pressing: The powder mixture is compacted in a mould under high pressure. This method is suitable for simple geometries and allows for good dimensional control.
Isostatic Pressing: Both cold isostatic pressing (CIP) and hot isostatic pressing (HIP) use fluid pressure to form the green bodies. CIP uses rubber moulds at room temperature, while HIP applies heat during the pressing process, which can enhance the density and reduce porosity.
Slip Casting:
A liquid suspension of zirconia powder (slip) is poured into a porous plaster mould. The mould absorbs water from the slip, allowing a solid layer to build up against the mould surface. Once sufficient thickness is achieved, the remaining slip is poured out, and the formed crucible is allowed to dry.
Injection Molding:
Suitable for more complex shapes, this method involves injecting a heated mixture of ceramic powder and polymer binder into a mould. After cooling, the binder is removed through thermal decomposition or solvent extraction, leaving behind the shaped green body.
3. Drying
The green bodies (unfired parts) are carefully dried to remove any moisture or organic solvents used during shaping. This step is critical to prevent cracking during subsequent firing.
4. Sintering
Firing/Sintering: The dried green bodies are then fired at very high temperatures (typically between 1400°C and 1600°C) in a kiln or furnace. During this process, the particles fuse together, increasing the density and strength of the material. The stabilization additives help maintain the cubic or tetragonal phase of zirconia, enhancing its mechanical properties.
Controlled Atmosphere: Sintering may occur in controlled atmospheres (such as air, oxygen, or inert gases) to avoid unwanted reactions and ensure optimal material properties.
5. Machining and Finishing
Grinding and Polishing: After sintering, the crucibles may undergo machining to achieve precise dimensions and surface finishes. Diamond tools are commonly used due to the hardness of zirconia.
Surface Treatment: Additional treatments such as lapping or polishing can be applied to reach the desired surface finish, improving the aesthetic appearance and functionality.
6. Quality Control
Throughout the manufacturing process, quality control measures are taken to ensure that the crucibles meet specified standards for purity, density, strength, and other physical properties. This includes testing for chemical composition, mechanical strength, thermal stability, and dimensional accuracy.
7. Packaging and Handling
Finally, the finished zirconia crucibles are packaged carefully to prevent damage during shipping and handling. Instructions for proper use and care are often included to ensure users get the best performance from the product.
Applications of zirconia ceramic nozzles:
Injection Molding:
In injection moulding machines, zirconia nozzles are employed for feeding molten materials into moulds. Their resistance to wear and corrosion makes them suitable for handling abrasive or corrosive materials.
Metal Casting:
For pouring molten metals, especially in continuous casting processes, zirconia nozzles are utilized because they can resist the high temperatures and aggressive nature of metal melts without degrading.
Ceramic and Glass Manufacturing:
In these industries, zirconia nozzles are used for extruding ceramic pastes or glass melts. The nozzles maintain their shape and dimensions even under high-temperature conditions, which is critical for producing consistent products.
Abrasive Water Jet Cutting:
Zirconia nozzles serve as mixing chambers in abrasive water jet cutting systems. They mix water with abrasive particles at very high pressures to cut through hard materials like metals, ceramics, and composites.
Pharmaceuticals:
For precise dosing of pharmaceutical compounds during manufacturing, zirconia nozzles provide accurate delivery due to their smooth surface finish and non-reactive nature.
Aerospace:
In aerospace applications, zirconia nozzles can be found in thrusters and propulsion systems, where they must endure extreme temperatures and pressures.
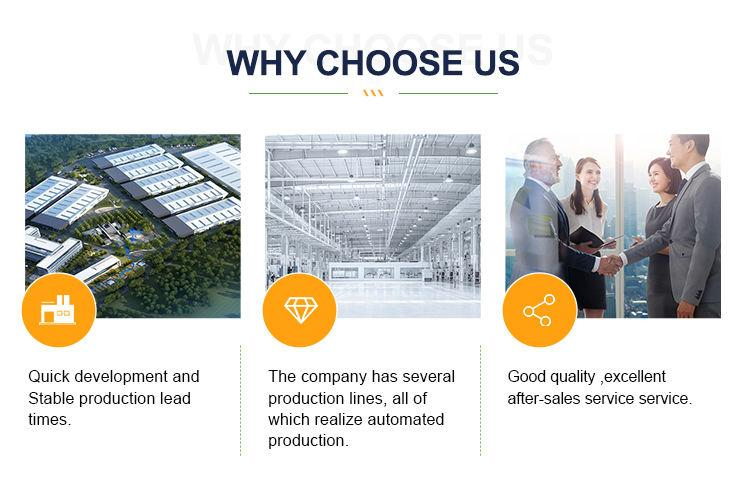
Company Profile
Advanced Ceramics founded on October 17, 2014, is a high-tech enterprise committed to the research and development, production, processing, sales and technical services of ceramic relative materials and products.. Since its establishment in 2014, the company has been committed to providing customers with the best products and services, and has become a leader in the industry through continuous technological innovation and strict quality management.
Our products includes but not limited to Silicon carbide ceramic products, Boron Carbide Ceramic Products, Boron Nitride Ceramic Products, Silicon Carbide Ceramic Products, Silicon Nitride Ceramic Products, Zirconium Dioxide Ceramic Products, Quartz Products, etc. Please feel free to contact us.(nanotrun@yahoo.com)
Payment Methods
T/T, Western Union, Paypal, Credit Card etc.
Shipment Methods
By air, by sea, by express, as customers request.
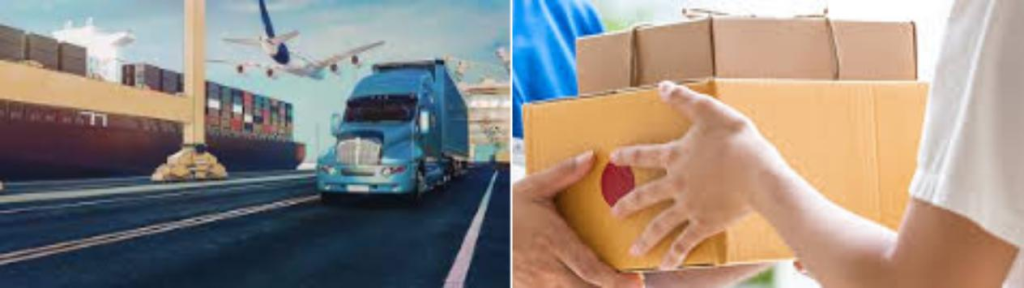
FAQs of Zirconia ceramic Crucible
1.How Do I Choose the Right Zirconia Nozzle for My Application?
A:Selecting the right nozzle involves considering factors such as operating temperature, chemical compatibility, pressure, flow rate, and material abrasiveness. Consulting with manufacturers or suppliers can help identify the best option.
2.How Should Zirconia Nozzles Be Cleaned?
A:Cleaning should be done carefully to prevent contamination and ensure longevity. Typically, this involves using appropriate solvents or cleaning agents followed by thorough rinsing and drying.
3.What Is the Expected Lifespan of a Zirconia Nozzle?
A:The lifespan depends on the application conditions, including temperature, material being processed, and maintenance practices. Regular inspections and proper care can extend service life.
4.What Are the Temperature Limits of Zirconia Nozzles?
A:Zirconia can withstand very high temperatures, typically up to around 2700°C, depending on the stabilization method and additives used. However, practical operating temperatures are usually lower, based on the application.
5.How Do Zirconia Nozzles Handle Thermal Shock?
A:Zirconia has relatively low thermal conductivity and a low coefficient of thermal expansion, which helps it resist thermal shock better than many other refractory materials. However, rapid temperature changes can still cause damage if not managed properly.
REQUEST A QUOTE
RELATED PRODUCTS
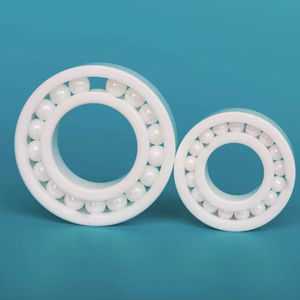
0.1mm-50mm 95 Zirconia Dioxide Yttrium Oxide Stabilized Ball ,ceramic Beads for Jewelry Polishing Zro2 Ceramic Ball 45%
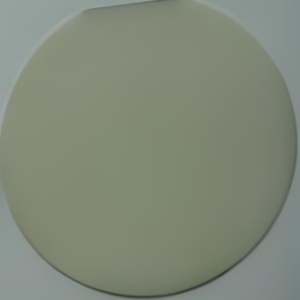
Very Thin Zirconia Black Ceramic Sheet Substrate Surface Polishing Round Zirconium Oxide Ceramic Plate
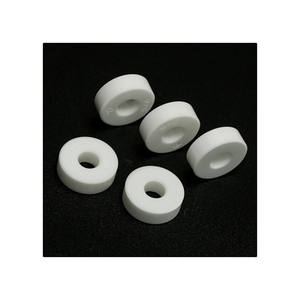
High Polishing 3 Mol Yttria Stabilized ZrO2 Zirconia Zirconium Oxide Ceramic Crucible Mug / Cup For Melting
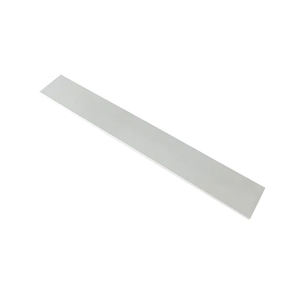
Stabilized Zro2 Zirconia Zirconium Oxide Ceramic Sheet for Sinter
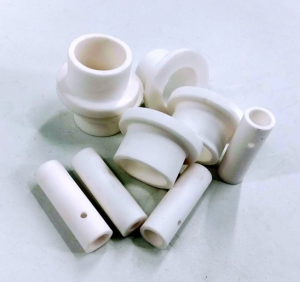
High Wear Resistance Zirconia Ceramic Tube ZrO2 Ceramic Pipe
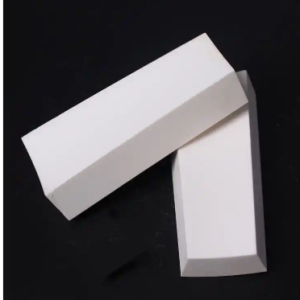